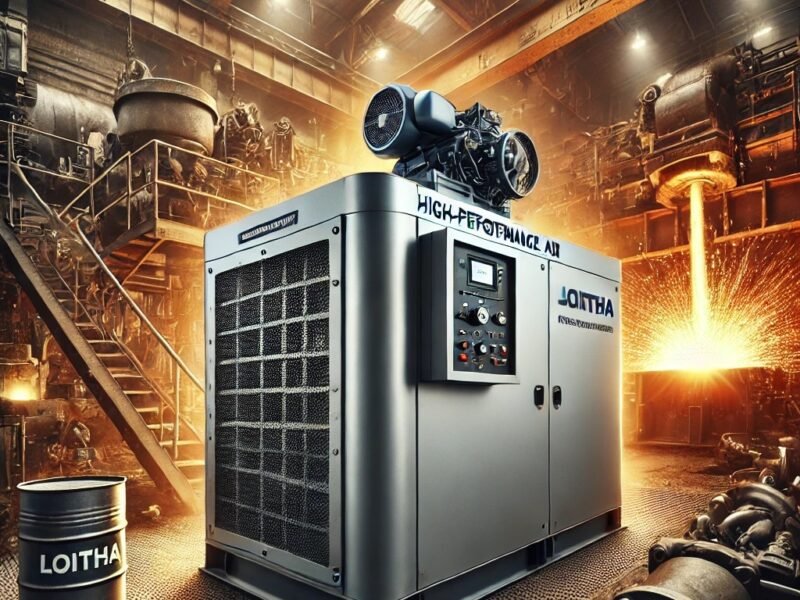
The Loitha Screw Air Compressor is engineered specifically for the demanding needs of casting and forging operations. Its high efficiency, durability, and ability to provide a consistent supply of compressed air make it an ideal solution for powering pneumatic tools, machinery, molds, and maintaining effective cooling and cleaning processes.
Compressor for Casting and Forging
Key Features for Casting and Forging
- High Efficiency
- Loitha screw compressors utilize energy-saving technology to minimize electricity usage while maintaining a steady airflow. Their high-efficiency motors and advanced components significantly lower operational costs, making them ideal for energy-intensive industries such as casting and forging.
- Continuous Operation
- The casting and forging processes necessitate compressors that can function without interruptions. Loitha screw compressors are designed for continuous duty, providing a reliable supply of compressed air throughout long production shifts, thereby maximizing productivity without downtime.
- Durability and Reliability
- Built to withstand the harsh conditions typical of casting and forging environments, Loitha compressors are robust enough to endure extreme temperatures, heavy mechanical loads, and dust. Their sturdy construction guarantees dependable performance over time, even in challenging operating conditions.
- Low Maintenance
- With fewer moving parts compared to traditional piston compressors, Loitha screw compressors require less maintenance. This leads to longer service intervals and reduced downtime, helping keep production lines running smoothly.
- High Air Delivery
- The casting and forging industries demand substantial volumes of compressed air for operating pneumatic tools, presses, hammers, and other machinery. Loitha compressors provide high-volume, high-pressure air to ensure optimal performance, efficiency, and consistent output in demanding settings.
- Air Quality Control
- Maintaining the quality of compressed air is vital in casting and forging industries to prevent contaminants from affecting mold integrity, product quality, and machinery performance. Loitha compressors include integrated air treatment systems, such as filters and dryers, ensuring the air is clean, dry, and free of harmful moisture and particles.
- Compact Design
- Loitha screw compressors are designed with space efficiency in mind, making them suitable for installations in confined spaces common in casting and forging facilities. Despite their compactness, they deliver optimal performance without sacrificing capacity.
- Quiet Operation
- While industrial environments are often noisy, Loitha compressors are designed with noise-reducing features, making them significantly quieter. This not only improves the overall working environment but also enhances employee safety and comfort.
“Efficiency is doing better what is already being done. “
-Peter Drucker
Benefits for Casting and Forging
Enhanced Process Efficiency: By delivering a consistent supply of high-quality compressed air, Loitha compressors improve the performance of pneumatic tools, machines, and mold handling equipment, thereby optimizing casting and forging operations.
Cost Savings: The energy-efficient design and low maintenance requirements help reduce operational costs, making Loitha screw compressors a cost-effective choice for casting and forging industries.
Durability and Reliability: Built to endure the demanding conditions of casting and forging operations, these compressors minimize the risk of downtime and ensure reliable performance over time.
Optimized Safety and Air Quality: With integrated air treatment systems, Loitha compressors guarantee clean, dry, and contaminant-free air, safeguarding sensitive equipment, maintaining product quality, and reducing the likelihood of operational disruptions due to air quality concerns.
The Loitha Screw Air Compressor is an invaluable asset in casting and forging operations, offering energy efficiency, continuous operation, and superior air quality control. Its durability, low maintenance requirements, and compact design provide a cost-effective and reliable solution, optimizing the production process while minimizing downtime and operational expenses.